With the popularity of portable devices like smartphones and tablets, Power Delivery (PD) and Quick Charge (QC) charging products have attracted attention from consumers. Car charger adapters use electricity generated by the car to charge portable devices. These products have become indispensable in our cars nowadays.
Although PD/QC charging products bring convenience to users, these products also have many issues. In this article, Allion has compiled data and research for you. We’ll be looking at the PD/QC car charger adapters sold on Amazon and Walmart and their most common issues reported by actual users.
Structural Issues
Structural issues are mainly related to the physical design of the product. This problem accounts for 29% of all issues. Some manufacturers will design their chargers to be too small or have the sockets too close to each other for aesthetic purposes, making it difficult for users to plug or unplug cables. Sometimes it needs an awkward force or finger placement to do so successfully. Between the car chargers and the base of the console, some designs make it difficult to plug in and out because of tightness, and some designs make it difficult for the cables to stay in because it’s too loose.
These situations can easily lead to usability issues and negative feedback. Allion has designed a questionnaire based on six different car charger adapters in the market for our engineers to conduct blind tests. With the participants having different usage habits, we tried to use an objective perspective to test how users felt about the tightness and looseness of the products.
Next, we used an SUV in the market as a testing example and measured everything around the car charger port. We used six different car charger adapters for this experiment. Since the design of each car is different and the charging port is usually placed within a space resembling a trapezoid, a compact design for this product might not be a better choise. Of course, this will depend on which car and which car charger adapter you are using. Both need to be perfectly designed to provide consumers with a good user experience.
According to the results above, it can be seen that the M brand and the B brand had better performance. They both had relatively better scores regarding the console and armrest. Although the width of the product and its protrusion length were not the worst, the C brand had the worst overall score of all. Additionally, the car charger sockets felt too tight, which means it will be difficult to plug and unplug in smaller spaces.
Charging Issues
Charging issues account for 24% of all issues. Though fast charging can save users a lot of time, some PD/QC chargers have slow charging issues. This could be related to the charging cables, the power of the charger, communication protocols between the products, and others. In general, consumers are concerned about chargers that claim to support fast charging but cannot do so in actuality.
Durability Issues
When a newly purchased car charger breaks just after buying, would you stop using that brand? Durability is also an important aspect that consumers are concerned about, accounting for 15% of the issues above. To reduce costs, some manufacturers will choose to use low-quality components with simple circuit designs, which results in more product malfunctions. When users experience this, it negatively affects the user experience and could also cause damage to the charger.
Quality Control Issues
Quality control issues account for 14% of all issues. Consumers have claimed that they cannot charge their devices just after receiving them. Manufacturers must try their best to avoid this issue during the production phase. Once this occurs, it’s followed by a large number of negative reviews and complaints from consumers who want to return their products. This will inevitably cost a lot of money to fix, but also negatively impact your company’s brand image and product positioning.
Compatibility Issues
Compatibility issues refer to the issues between the car charger adapter and the device that needs charging. This is similar to the charging speed issue, but it mainly consists of certain devices that cannot be charged. For example, Samsung or Apple phones cannot be charged due to compatibility issues. These issues account for 8% of all issues. Since charging specifications of devices are usually complex, different versions of products may be incompatible with specific charging products. Users often need to replace the charger or charging cable, making it increasingly inconvenient and costly for them. When users experience this, they will want to return these products. If manufacturers can provide the charger with multiple PD profiles, it can greatly reduce the chance of this issue occurring.
Fuse Issue
This issue accounts for 6% of the issues above. The car charger might overheat when charging at high power for long periods, or the car could suddenly generate excessive voltage or current, triggering the protection mechanism of the product which results in a burnt fuse. Car chargers have this mechanism to ensure safety for the users.There are two ways this can happen. Either the product’s fuse is burnt and cannot be used any longer, or the car’s fuse is burnt and the product is fine. If the product’s fuse is burnt and isn’t designed to be replaced, it will immediately become e-waste and the user will want to replace it if it’s still within the warranty period, increasing production costs.If the car’s fuse is burnt, the users will have to go to a repair center to fix their car’s fuse, wasting extra money and time, and most importantly damaging the brand image of your company. This is a very important issue that manufacturers and brands need to pay attention to.
Other Issues
This category is filled with other issues that consumers rarely encounter, accounting for 4% of the total issues. Issues like overheating, smoke, interference with electronic devices (TPMS, GPS, radio), accessory issues (no charging cable included), lack of charging light, sockets cannot simultaneously charge, and others.
Although the percentage is low, there are still some issues that require attention. The product overheating and smoking could easily cause danger to drivers and passengers. If something were to happen to users’ lives and property, manufacturers would be looking at huge lawsuits. Such asTPMS, may lead to unnoticed low tire pressure, raising safety concerns during driving. GPS navigation interruptions can also inconvenience users. These issues should be avoided and prevented by running sufficient product testing and verification during the product development stage.
In Allion’s experience, the most common issue with car charger adapters is that they lack certain charging modes, resulting in different performances with different products that users own. For example, a company advertises its product to support Apple 2.4A charging, but this charging mode is nowhere to be seen when tested. Another example would be the metal components are stuck after being plugged and unplugged.
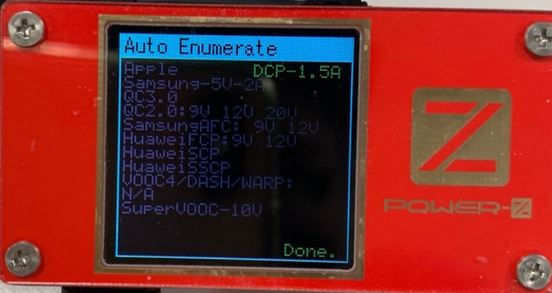
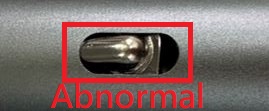
Situations like this where the metal component is stuck should be taken care of during the product design phase because once this issue occurs, they will want to return it and replace it. Even if the user doesn’t want to return it and finds a way to fix it, this situation can easily happen again. This will affect the user experience and their willingness to purchase these products once again.
Conclusion
To ensure the charging efficiency and safety of in-vehicle chargers, manufacturers need to be thorough in product design and production. Before formal shipments, they must identify and address the concerns most likely to arise for consumers. Furthermore, rigorous quality testing and relevant certifications are essential. Additionally, the shipped products must have clear labeling, product usage instructions, and safety guidelines to ensure that consumers can use the product safely and achieve fast charging effects. Because in-vehicle chargers are one of the indispensable products for driving, Allion Labs can provide the following testing services for in-vehicle chargers:
- Compatibility Test)
- Functionality Test)
- Stability Test)
- User Experience Test)
- Competitive Analysis and Consulting)
Allion can conduct customized tests and verification planning for various products, participate in the early stages of product development, and assist clients with producing high-quality products. Allion has a complete set of testing equipment such as laptops, mobile phones, tablets, and more. With our complete range of equipment of various brands, we can provide the best quality control for our clients!