New Digital Teaching Tools: Interactive Displays
In the post-pandemic era, nations are prioritizing economic recovery and development, with a strong emphasis on transforming education systems to foster cultural understanding, diversify learning modalities, and promote self-directed learning. As a result, a new educational model is emerging, characterized by a deeper level of student engagement through interactive learning techniques. Central to this transformation is the adoption of interactive touch displays, which are revolutionizing teaching methodologies and enhancing the learning experience.
Interactive displays are widely used in schools, enhancing the interactivity and engagement of teaching. Educators leverage these displays to deliver content more intuitively, using touch-based gestures to create a dynamic and engaging teaching environment. These devices serve not only as replacements for traditional blackboards and whiteboards but also as versatile digital platforms that facilitate handwriting, drawing, and real-time content modification. Additionally, the ability to integrate multimedia resources—such as videos, images, and web content—broadens the scope of instructional materials, enabling a greater learning experience for students.
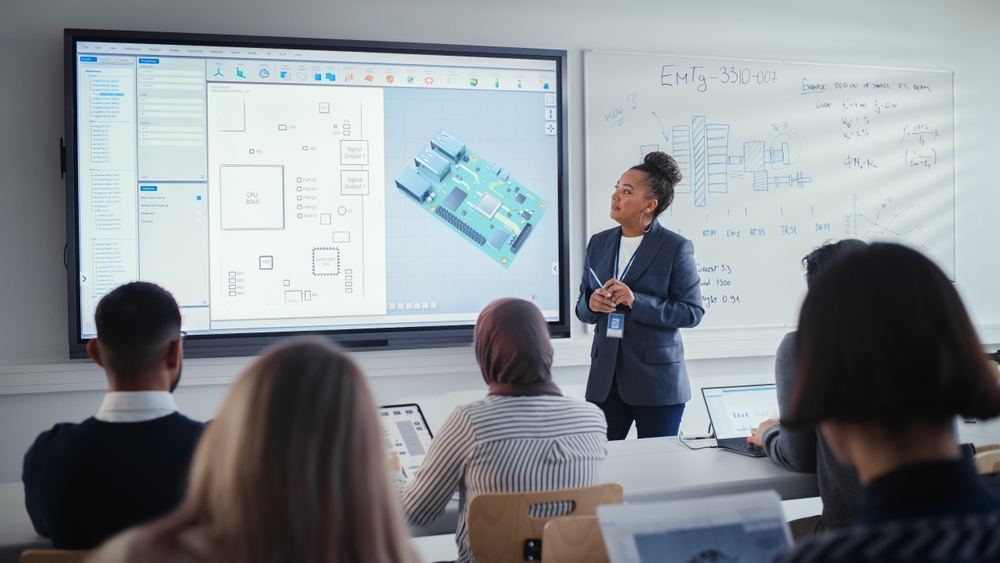
Interactive Display Technology
The technology integrated into interactive touch displays has reached a level comparable to that of smartphone screens. In addition to supporting multi-touch, these displays facilitate interactive learning in classrooms. Educators can utilize built-in applications to prepare teaching materials, integrating relevant articles and images into their lessons. The displays support video output and touch connectivity by connecting to laptops or desktop computers via USB Type-B to USB Type-A cables to enable full functionality across devices.
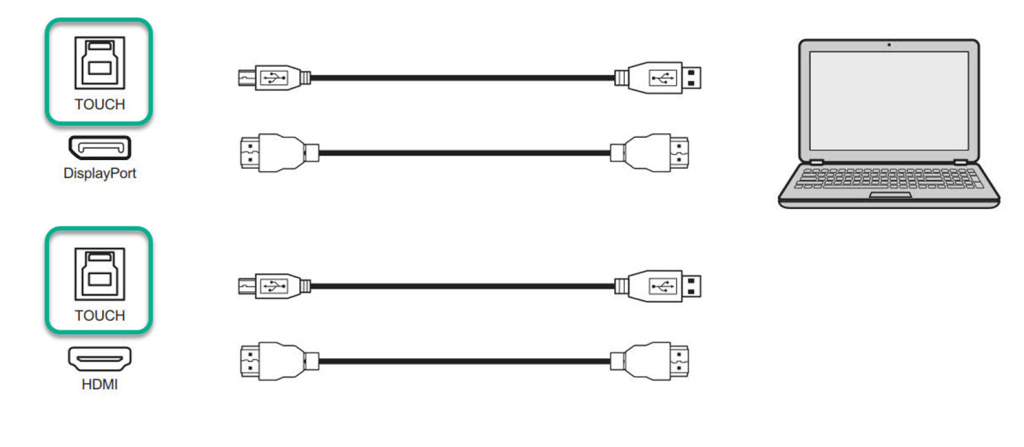
USB cables—such as USB 3.1 Type-B to Type-A—play a critical role in enabling the touch functionality of interactive displays. The selection and rigorous testing of cable quality are crucial to ensuring reliable touch performance, particularly due to the stringent requirements for crosstalk interference in high-speed signal transmission. Poor cable quality can negatively impact the user experience and teaching effectiveness. It may also jeopardize the market image and reputation of brand image of the display manufacturer.
Customer Issues and Challenges
A brand of interactive displays has products widely used in education and marketing, capable of easily playing high-resolution videos and quickly connecting to various digital devices. However, after selling the products, some customers reported issues that seemed to arise from the quality of the randomly included USB cables or the USB ports of the displays, leading to image display discrepancies and subsequently affecting teaching effectiveness and overall user experience. The main issues observed are as follows:
Insufficient Touch Accuracy: Users frequently experience false touches or inaccurate operations, affecting teaching efficiency.
Screen Flickering and Shadows: Abnormal flickering and shadows occur on the display during touch operations, disrupting the visual experience.
Inconsistent Response Times: Response times vary across different touch areas, resulting in uneven operation and affecting teaching synchronization.
Key Challenges Faced by the Brand
- Lack of Technical Expertise: As the brand primarily focuses on the development and sales of displays, it lacks in-depth knowledge of cable and connector technology. This gap in understanding the importance of USB cables and connectors for image quality and touch accuracy makes it difficult to identify and resolve these technical issues.
- Complexity of Issues: Problems like insufficient touch accuracy, screen flickering, and inconsistent response times may involve multiple factors, including cable quality, connector design, and signal interference. Without professional testing equipment and experience, it is hard for the brand to accurately identify the root causes.
- Supply Chain Management Challenges: The brand lacks the ability to effectively evaluate and select high-quality cable suppliers. They are unaware of the differences among various USB cables and how these differences affect product performance.
- Adapting to Evolving Standards: As USB standards continue to evolve, the brand struggles to keep up with the latest specifications, making it difficult to choose suitable cables for their products.
- Quality Control Constraints: Without access to professional testing processes and equipment, the brand cannot effectively conduct quality control for cables and connectors, leading to substandard products entering the market.
- Cost-Benefit Considerations: Establishing an in-house team to address these issues would be costly and diverge from the brand’s business focus.
- Customer Satisfaction Risks: Ongoing product issues could severely impact customer satisfaction and brand reputation, necessitating rapid and effective solutions.
- Market Competition Pressure: In a highly competitive market, the brand needs to focus on core product development and marketing strategies, rather than getting sidetracked by technical details.
To address these challenges, the brand requires an external partner with specialized expertise in cable and connector. After recognizing our capabilities in this area, they reached out to us for technical support and assistance in the following areas:
- Accurately diagnosing: Identify the root causes of technical issues.
- High-quality component selection: Help select standard-compliant cables and connectors.
- Quality control implementation: Establishing effective testing and quality control processes
- Issue resolution: Providing solutions to current issues and enhancing product quality
- Strategic focus: Allowing the brand to focus on its core business.
- Customer satisfaction enhancement: Improving customer satisfaction and brand image
By partnering with Allion, the brand can effectively resolve current technical problems while receiving long-term technical support and quality assurance. After detailed discussions with the brand, we assisted in analyzing the issues and provided the following solutions.
Root Cause Analysis
Specification Noncompliance: Although the cables were labled as USB-compliant, actual performance tests revealed that they did not meet required standards, leading to unstable signal transmission.
Variations in Electrical Characteristics: Samples exhibited inconsistent electrical characteristics, leading to inconsistencies in cable quality.
Environmental Interference: External factors such as electromagnetic interference can also affect the stability of signal transmission.
Solutions
- Supply Chain Quality Management:
- Choosing Certified Vendors: We recommend that the customer prioritize selecting cable and connector suppliers certified by USB-IF to ensure product quality and reliability.
- Establishing an Approved Vendor List (AVL): We assist the customer in creating stricter quality requirements based on certification standards, inviting multiple suppliers to submit product samples. These samples are then compared and evaluated to identify the best options.
- Comprehensive Sample Testing: Allion conducts rigorous performance testing on samples from suppliers to confirm that they meet high-quality standards within acceptable error margins.
- Improved Testing and Verification:
- Establishing Robust Testing Processes and Methods: We implement comprehensive testing during the production process, including functionality, performance, and reliability testing, to ensure all performance indicators meet standards.
- Simulating Real-World Environments: We conduct tests under simulated real-world conditions to validate the stability and reliability of the products in actual operating scenarios.
- Introducing AI Automated Testing:
- Implementing AI Testing Solutions: We recommend that the customer’s cable and connector suppliers use the AI automated testing solution (Allion Cable-Connector Multiport System, ACMS) for outgoing quality control (OQC), enhancing testing efficiency and accuracy to ensure product performance consistency and high standards.
Explore more: Allion Cable-Connector Multiport System (ACMS)
Through the implementation of our proposed solutions, the brand successfully replaced the previous cables with standard-compliant, high-quality USB cables. Additionally, we established a rigorous quality management system for the cable and connector supply chain, ensuring that all future product selections adhere to high-quality standards. This initiative significantly improved the performance and reliability of the brand’s products.
Creating Value for You
Time to Market with Quality!
Faster! Easier! Better!
Allion is dedicated to providing comprehensive solutions and consulting services that empower clients to achieve superior product quality. Our expertise not only ensures the signal quality of USB transmission cables and connectors but also supports the establishment and optimization of quality management systems throughout the supply chain. Our core advantages include:
Faster
- Efficient Problem Diagnosis: Allion utilizes advanced testing equipment and expertise to quickly identify root causes, such as specification noncompliance, variations in electrical characteristics, and environmental interference.
- Rapid Solution Implementation: Through comprehensive supply chain oversight and testing verification processes, we swiftly provide feasible solutions to our clients.
- Accelerated Time to Market: By leveraging precise vector network analyzers and efficient testing processes, we significantly shorten product development and validation cycles, speeding up time to market.
- Real-Time Data Analysis: Through cross-comparison and vertical integration, we can quickly align with various USB specifications and customized measurement standards, providing immediate test results and analysis.
Easier
- One-Stop Solution: Allion offers a complete service from problem diagnosis to solution implementation, simplifying the workflow for clients.
- Supply Chain Management Support: We assist clients in establishing Approved Vendor Lists (AVL), streamlining supplier selection and management processes.
- Flexible Testing Services: We provide a variety of USB signal measurement services and testing fixture solutions, allowing clients to choose the services that best meet their needs.
- Professional Guidance: We offer advice on connector and PCB matching optimization and mechanical design, alleviating the technical burdens on clients.
- Automated Testing: We recommend implementing AI automated testing solutions (ACMS) to simplify testing processes and enhance efficiency.
Better
- Quality Enhancement: Through stringent testing and verification processes, we ensure that products meet higher quality standards.
- Performance Optimization: Comprehensive testing and optimization recommendations improve various performance aspects of products, including signal stability and interference resistance.
- Supply Chain Optimization: We assist clients in selecting certified vendors and establishing higher quality standards, enhancing overall supply chain quality.
- Comprehensive Compatibility: We ensure that products are compatible with various devices and environments, improving user experience.
- Technological Leadership: Through thorough testing and optimization services, we help clients maintain a technological edge.
- Long-Term Value: We establish a robust quality management system, creating long-term competitive advantages for clients.
Partnering with Allion allows clients to resolve immediate technical challenges and ensure products meet high quality and performance standards. This not only enhances market competitiveness but also provides significant benefits to end users, driving technological progress and innovation in the industry, ultimately achieving the goal of “Time to Market with Quality.”
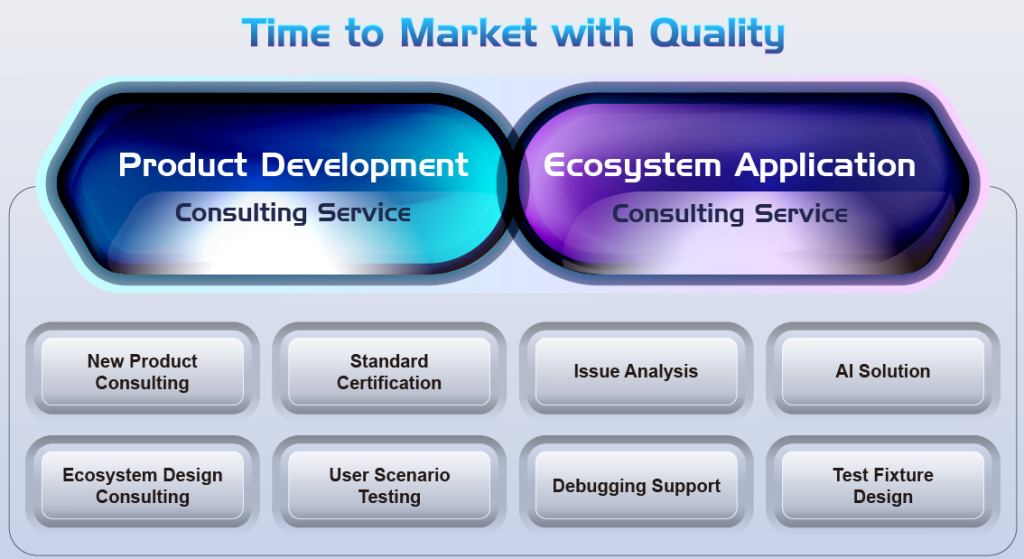