Application Environment and Customer Needs
As technology continues to advance, 6K and 8K displays are gradually becoming the trend, redefining our expectations for image quality.
The attention on 6K and 8K displays is mainly due to their extremely high resolution. For example, a 6K display has a horizontal resolution of over 6,000 pixels, significantly enhancing image detail and clarity, allowing users to experience a more immersive visual effect. The 8K display takes detail to the next level, providing users with an even more immersive experience.
However, the widespread adoption of high-resolution displays brings challenges, primarily related to increased hardware requirements. High resolution necessitates more powerful processors and graphics cards. Currently, 6K/8K displays primarily use the latest DisplayPort 2.1 (DP2.1) or HDMI 2.1 specifications, meaning the entire ecosystem, including cables and graphics cards, must support these latest standards.
Nevertheless, even with hardware that supports DP 2.1 or HDMI 2.1, if the cables used are problematic, consumers may still face risks of improper high-resolution display. This situation highlights the importance of performing IQC (Incoming Quality Control) testing. IQC testing ensures that every audio-visual cable meets quality standards, preventing non-compliant cables from causing issues with high-resolution displays or resulting in image quality problems.
This article shares a case involving a major display manufacturer that experienced image quality issues. Analysis revealed that the problem was with the cables shipped together with the product. Therefore, they sought Allion’s assistance to ensure that users could fully enjoy the visual benefits of high-resolution displays and meet consumer expectations for high-quality products.
Customer’s Problems and Challenges
High-resolution displays have stricter quality requirements for cables, as they need to transmit large amounts of data to render detailed images. Poor-quality cables can lead to image distortion, delays, or even connection failures.
In this case, the customer, who focuses on high-end high-resolution displays, discovered intermittent issues with 6K and 8K image display before mass production. These issues did not occur during the early development phase. After extensive internal cross-checking, it was found that the problem might lie in the inconsistent quality of the DP cables shipped with the product. Poor-quality transmission cables led to decreased transfer speeds, affecting the image playback quality and gaming experience for users. The customer intended to perform a comprehensive inspection of the shipped DP cables but encountered the following difficulties and challenges in achieving 100% inspection:
- Lack of Expertise and Capability: Conducting 100% IQC cable testing involves tests of electrical performance and signal transmission capabilities, requiring specialized knowledge and skills for accurate execution. For manufacturers focused primarily on product manufacturing, this represents expertise in another domain.
- Lack of Appropriate Testing Equipment: Specialized testing equipment is required to fully conduct IQC inspections, such as oscilloscopes and network analyzers.
- Lack of Appropriate Fixtures: Cable inspection also requires matching testing fixtures. If customers lack expertise in the cable domain, it is even more challenging to develop and design fixtures.
- Complex, Time-Consuming, and Labor-Intensive Testing Process: Achieving 100% IQC inspection is a complex process. It involves creating suitable test plans based on different cable specifications and requirements, as well as analyzing and organizing test data, which requires significant manpower.
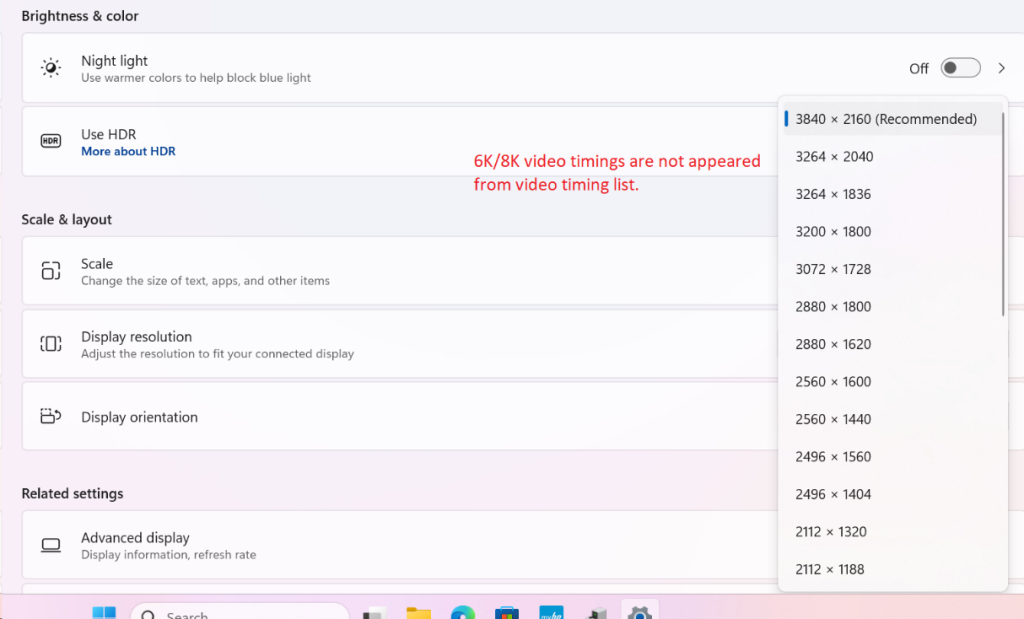
Solution
The main issue in this case is that the quality problems with some cables were not due to design flaws but rather instability during the mass production process. For manufacturers, the biggest challenge is to conduct comprehensive inspections of all cables in a short period to exclude defective ones, preventing end users from experiencing poor performance that could be mistakenly attributed to the display itself. The Allion team understands the difficulties faced by manufacturers and, therefore, proposed a solution that can perform comprehensive cable testing in a short time to achieve 100% cable IQC inspection.
Understanding the time and effort required for manual verification of cables and connectors, the Allion consulting team developed the automated solution Allion Cable-Connector Multiport System (ACMS). ACMS integrates network analyzers, fixture design, and automated software development, significantly reducing verification time while ensuring consistency in testing, making 100% cable inspection feasible.
Below is a comparison of the differences between Allion’s use of ACMS for 100% inspection and manual verification:
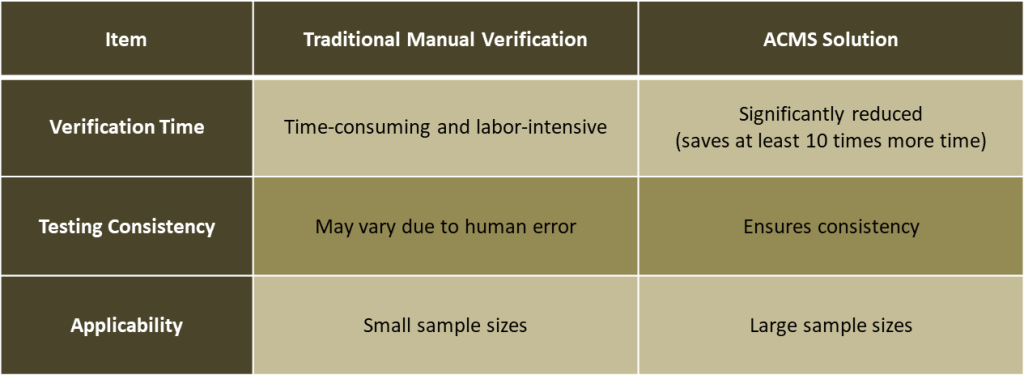
The table below compares the time required for testing a large number of samples using manual methods versus the ACMS solution, using DP cables as an example.
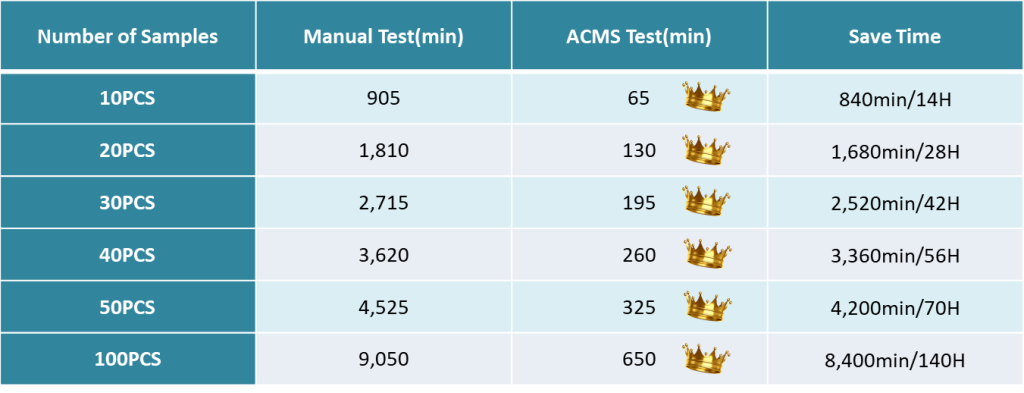
Time to Market with Quality! High-Quality Service to Create Value for You
Faster, Easier, Better!
ACMS Testing Solution: Helping You Achieve 100% IQC Inspection and Create High-Quality Products
In a highly competitive market environment, manufacturers face increasing pressure to ensure product quality while also improving efficiency and reducing costs. Traditional manual testing of cables and connectors is not only time-consuming and labor-intensive but also prone to human error and lacks scalability to meet growing production demands.
ACMS testing solution offers an effective resolution to these challenges, helping manufacturers achieve unprecedented levels of quality assurance and production efficiency.
Faster
Unlock Speed Potential:
- ACMS uses automation to accelerate the testing process, achieving nearly 14 times the testing speed compared to traditional manual methods. This enhanced efficiency translates to shorter testing times, faster time-to-market, and a competitive edge in the market.
Easier
Easily Handle Various Needs:
- ACMS supports a wide range of cable and connector standards, including USB, DP, HDMI, and Thunderbolt. Additionally, Allion’s customization capabilities allow adjustments based on your specific testing requirements, ensuring comprehensive coverage and compatibility.
Optimize Testing Processes:
- Allion provides a comprehensive one-stop solution, including fixture design and manufacturing, simplifying your testing processes, eliminating the need for external resources, and ensuring a smooth and efficient testing experience.
Achieve 100% Inspection:
- ACMS allows you to configure custom test items based on your specific needs, enabling true 100% inspection. This comprehensive testing approach ensures that every cable meets the highest quality standards, eliminating the risk of defective products reaching customers.
BetterBetter
Enhance Quality and Reliability:
- By minimizing human intervention, ACMS ensures consistency and reliability in testing results. Automated testing eliminates the possibility of human error, subjecting each cable to rigorous and consistent quality checks.
Timely Defect Detection and Brand Protection:
- ACMS solution enables timely identification of defective cables and connectors, protecting your brand reputation and minimizing product recalls through a proactive approach.
If you have any questions or requirements, please contact us.